Cementownia Chełm
Cementownia zlokalizowana jest w Chełmie. Jest producentem cementów portlandzkich, portlandzkich popiołowych, portlandzkich wieloskładnikowych np. popiołowo-żużlowych oraz cementów specjalnych niskoalkalicznych i odpornych na siarczany, w tym dla budownictwa infrastrukturalnego, np. CEM I 42,5 R – SR 5/NA. W roku 2023 zakład wybudował instalację i uruchomił produkcję, hydraulicznego spoiwa drogowego o handlowej nazwie „Connecton HSD E 24”. Produkcja tego spoiwa i ocena właściwości użytkowych, odbywa się w oparciu o uzyskaną wcześniej Krajową Ocenę Techniczną. Wszystkie te działania związane są z dążeniem do uzyskania neutralności klimatycznej naszych produktów. CEMEX Polska, jako pierwszy z polskich producentów cementu, w roku 2022 uzyskał i opublikował deklaracje środowiskowe III Typu, tzw. EPD na wszystkie swoje produkty.
W roku 2008 w Cementowni Chełm wdrożono Zintegrowany System Zarządzania, na który składają się System Zarządzania Jakością (ISO 9001), System Zarządzani Środowiskowego (ISO 14001), System Zarządzania BHP (ISO 45001) oraz System Zarządzania Energią (ISO 50001). Dodatkowo w roku 2011 zakład został wpisany do - prowadzonego przez Generalną Dyrekcję Ochrony Środowiska – rejestru EMAS. Fakt ten potwierdza spełnienie najwyższych standardów w zakresie ochrony środowiska, co corocznie potwierdzane jest przez niezależnych weryfikatorów.
W Cementowni Chełm funkcjonuje Zakładowa Kontrola Produkcji zgodna z wymaganiami normy PN-EN 197-1 a w ostatnim czasie zakład uzyskał także certyfikat KZR INiG zapewniający przedsiębiorcom uczestniczącym w łańcuchu produkcji biopaliw i biopłynów potwierdzenie spełnienia kryteriów zrównoważonego rozwoju (KZR) zgodnie z wymaganiami Komisji Europejskiej
Historia cementowni Chełm
Zakład Cementownia Chełm jest producentem cementu od 1960 roku. Wtedy zostały uruchomione pierwsze piece firmy F.L.Smith pracujące metodą mokrą. Szybki wzrost zapotrzebowania na cement zaowocował w 1970 r. rozbudową zakładu o kolejne piece metody mokrej. Kolejnym etapem modernizacji zakładu była budowa nowoczesnej linii produkcji klinkieru metodą suchą.
Klinkier w Chełmie produkowany jest na linii technologicznej, której rozruch odbył się w II poł. 1999 roku. Jest to linia metody suchej zaprojektowana przez duńską firmę F.L.Smidth. Ten piec był pierwszą pracującą w Polsce instalacją klinkierową zaopatrzoną w kalcynator. Dzięki temu przy swoich niewielkich wymiarach piec osiąga wysoką wydajność (5300 t/dobę). W ślad za wysoką wydajnością idą niskie wskaźniki emisji pyłów i gazów oraz niskie koszty produkcji. Linia jest stale modernizowana.
Piec jest również unikalny z innego powodu. Jest to typowy piec metody suchej, ale nie posiada silosów mąki surowcowej, a jako młyn surowca, stosuje suszarko-kruszarkę. Takie rozwiązanie spowodowało, że obsługa linii piecowej jest bardziej skomplikowana – dział surowcowy jest tutaj zintegrowany z linią piecową. Z drugiej strony spowodowało to znaczne uproszczenie techniczne i redukcję kosztów operacyjnych.
Technologia produkcji cementu w Cementowni Chełm
Do produkcji klinkieru wykorzystuje zarówno surowce naturalne jak i pochodzenia odpadowego z innych gałęzi przemysłu. Głównym składnikiem zestawu surowcowego jest kreda, pochodząca z własnej kopalni pozostałe surowce jak glina, piasek, popioły wapienne, dodatki żelazonośne, wapno pokarbidowe czy żużle pohutnicze, pozyskiwane są na rynku. Obecnie coraz większego znaczenia zyskują tzw. surowce zdekarbonizowane (DRM), które zawierają w swoim składzie wapno w postaci niewęglanowej. Są one doskonałym substytutem wapienia naturalnego, a wapno w takiej formie nie emituje już CO2 w procesie produkcji klinkieru cementowego. Udział tych surowców sięga już od kilku do kilkunastu procent w masie zużywanych składników. Wykorzystywanie kredy, jako bazowego surowca do produkcji klinkieru (ponad 80%) powoduje, że klinkier produkowany w Chełmie posiada unikalne właściwości i spełnia wysokie wymagania jakościowe wytwarzanych z niego cementów.
Produkcja cementu odbywa się w młynach kulowych w obiegu zamkniętym. Główne składniki cementu – klinkier, lotny popiół krzemionkowy, granulowany żużel wielkopiecowy i gips syntetyczny, tzw. reagips z odsiarczania spalin, które są razem mielone do czasu uzyskania odpowiedniego stopnia rozdrobnienia. Podczas mielenia stosuje się także różne dodatki ułatwiające przemiał czy reduktor chromu (VI), w zależności od typu produkowanego cementu. Cement jest wyrobem produkowanym zgodnie odpowiednimi specyfikacjami technicznymi, co w tym przypadku stanowią normy europejskie i krajowe: PN-EN 197-1, PN-B-19707 i PN-EN 197-5.
Zgodnie z wymaganiami zakładowej kontroli produkcji, dla zapewnienia odpowiedniej jakości produkowanego cementu, na każdym etapie stosuje się kontrolę międzyoperacyjną produkcji jak i kontrolę gotowego wyrobu.
Zakład kontynuuje politykę minimalizacji wpływu na środowisko naturalne, poprzez redukcję tzw. wskaźnika klinkierowego w cemencie i ograniczenie emisji CO2. Wprowadzone nowe rodzaju cementu pozwalają na zmniejszenie zawartości klinkieru w cemencie, z ilości ok. 90% w przypadku CEM I, do ilości ok. 62% w przypadku CEM II, a w przypadku spoiwa jest to ok. 30%. Takie podejście przyczynia się do istotnego zmniejszenia jednostkowej emisji na tonę gotowego produktu .
Zakład posiada dwa magazyny klinkieru o pojemności 250 tys ton, była to ważna inwestycja z punktu widzenia ograniczenia niekorzystnego wpływu na środowisko.
W cementowni znajduje się 12 silosów cementu o pojemności 5000 ton każdy. Zakład posiada 2 linie pakowania i paletyzowania cementu wyposażone w pakowaczki firmy Haver&Boecker oraz paletyzatory firmy Beumer. Dodatkowo obie linie wyposażone są w odpowiednie foliomaty.
Paliwa Alternatywne
Cementownia Chełm była jedną z pierwszych cementowni w Polsce, która zainwestowała w rozwój w zakresie spalania paliw alternatywnych, biorąc pod uwagę zarówno koszty produkcji, jak i aspekty ekologiczne.
Obecnie paliwa alternatywne są podstawowym źródłem energii cieplnej i ich udział w wytworzeniu energii potrzebnej do wypału klinkieru stanowi ponad 96%. Zakład wykorzystuje kilka rodzajów paliw alternatywnych dla których posiada odpowiednio przystosowane instalacji magazynowania oraz linie transportujące z układem dozującym. Są to paliwa typu RDF, mączka mięsno-kostna, pył gumowy i włókna z opon, suszone osady ściekowe oraz paliwa płynne. Odzysk termiczny zachodzi w instalacji w której temperatura gazów osiąga blisko 2000 oC, a czas przebywania w temperaturze powyżej 1000 oC wynosi kilka sekund. Tak wysoka temperatura oraz nadmiar tlenu i środowisko alkaliczne sprawiają że współspalanie paliw w procesie produkcji klinkieru zachodzi w sposób bezpieczny. Dodatkowo zakład wyposażony jest w odpylacz tkaninowy a emisja spalin jest monitorowana i musi spełniać standardy emisyjne które są określone w przepisach prawa. Jako pierwszy zakład w Polsce Cementownia Chełm zbudowała suszarnię do paliw typu RDF, która wykorzystuje w procesie suszenia ciepło odpadowe z procesu chłodzenia klinkieru. W skład instalacji paliw RDF wchodzi również separator powietrzny oraz precyzyjny układ dozujący.
Cementownia ściśle kontroluje jakość paliw alternatywnych tak, aby produkty powstające przy ich zastosowaniu, spełniały wymagania wszystkich restrykcyjnych norm. Obecnie Cementownia Chełm jest liderem w Polsce pod względem wykorzystania paliw alternatywnych.
Zarządzanie wpływem na środowisko
Procesy produkcji klinkieru i cementu prowadzone w Cementowni Chełm wywierają pewien wpływ na otoczenie, lecz naszym celem jest ograniczenie tego oddziaływania do minimum z wykorzystaniem różnych dostępnych narzędzi. Główną rolę w tym procesie odgrywa funkcjonujący w zakładzie od wielu lat, regularnie certyfikowany System Zarządzania Środowiskowego zgodny z normą ISO 14001:2015, a także system ekozarządzania i audytu zgodny z wymogami rozporządzenia EMAS. Sprawnie działający system pozwala nam zidentyfikować kluczowe oddziaływania, zaplanować ich redukcję, a także prowadzić procesy produkcyjne w zgodzie ze wszystkimi wymaganiami prawnymi i innymi. W celu zapobiegania emisji zanieczyszczeń, ścieków i odpadów, a także zużycia surowców naturalnych stosujemy przede wszystkim praktyki operacyjne mające na celu optymalizację procesów. Dodatkowo wspieramy się urządzeniami ograniczającymi emisję jak wysokosprawne odpylacze tkaninowe, elektrofiltr, biologiczna oczyszczalnia ścieków, system wewnętrznego odzysku odpadów technologicznych (pyłu z bypass’u).
Zakład działa w oparciu o szereg decyzji administracyjnych regulujących różne obszary jego funkcjonowania. Z perspektywy ochrony środowiska naturalnego oraz zapewnienia komfortu życia okolicznych mieszkańców kluczową decyzją jest tzw. pozwolenie zintegrowane dla instalacji wydawane przez Urząd Marszałkowski Województwa Lubelskiego. Określa ono podstawowe warunki i ograniczenia działalności zakładu w kontekście ochrony środowiska naturalnego, w szczególności dopuszczalne ilości wytwarzanych odpadów, zrzucanych ścieków oraz poziomy emisji zanieczyszczeń do powietrza.
Potwierdzenie spełnienia norm emisyjnych określonych w pozwoleniu zintegrowanym odbywa się zgodnie z rozporządzeniem w sprawie wymagań w zakresie prowadzenia pomiarów wielkości emisji z dnia 7.09.2021 r. Akt ten nakłada na cementownię obowiązek prowadzenia pomiarów emisji pyłu oraz innych wybranych zanieczyszczeń pochodzących z procesu współspalania odpadów w trybie ciągłym oraz pomniejszych zanieczyszczeń w trybie okresowym (tj. 2 razy w roku). W związku z tym na kominie pieca obrotowego - jedynym emitorze, z którego odprowadzane są gazy odlotowe z termicznego przekształcania odpadów, zainstalowany jest system monitoringu emisji pyłów i gazów, który mierzy poziomy emisji głównych zanieczyszczeń w trybie ciągłym. Instalacja do ciągłego pomiaru emisji podlega corocznym sprawdzeniom przez akredytowane laboratorium zewnętrzne. Sprawozdania z pomiarów ciągłych są przekazywane w cyklach półrocznych z uwzględnieniem danych dobowych, a z pomiarów okresowych – bezpośrednio po ich wykonaniu do Marszałka Województwa Lubelskiego oraz Wojewódzkiego Inspektora Ochrony Środowiska w Lublinie, Delegatura w Chełmie.
Poniżej umieszczono uśrednione wyniki pomiarów ciągłych emisji do powietrza dla poszczególnych kwartałów. Potwierdzają one pełną zgodność zmierzonych emisji z poziomami dopuszczalnej emisji określonymi w pozwoleniu zintegrowanym.
Emisje do powietrza z instalacji Cementownia Chełm - I kwartał 2024
Emisje do powietrza z instalacji Cementownia Chełm - II kwartał 2024
Emisje do powietrza z instalacji Cementownia Chełm - III kwartał 2024
Emisje do powietrza z instalacji Cementownia Chełm - IV kwartał 2024
Emisje do powietrza z instalacji Cementownia Chełm - I kwartał 2025
Emisje do powietrza z instalacji Cementownia Chełm - II kwartał 2025
Modernizacja Kopalni Kredy w Chełmie
W grudniu 2020 roku podpisano umowę na dostawę i montaż urządzeń do modernizacji kopalni. W ramach projektu zakupiono dwie koparki kołowoczerpakowe BWE 400, trzy przenośniki taśmowe na gąsienicach BW400, 3 przenośniki taśmowe B1000 (o długościach 360 m, 700 m i 1500 m), 2 kablozwiajki z zsypami mobilnymi oraz konieczną infrastrukturą energetyczną. Wartość inwestycji przekroczyła 10 milionów Euro.
Realizacja projektu, polegająca na wykonaniu fundamentów i montażu przenośników taśmowych, rozpoczęła się na terenie kopalni w wrześniu 2021 roku. Koparki i przenośniki mobilne zostały dostarczone w lipcu 2022 roku po czym rozpoczęto próbne rozruchy jednej koparki i dwóch przenośników na gąsienicach. Wydobycie dwoma koparkami kołowoczerpakowymi rozpoczęło się w październiku 2022 r.
Po okresie przejściowym od stycznia 2024 wydobycie jest prowadzone wyłącznie w nowym, zmodernizowanym systemie wydobycia tj. dwoma koparkami wielonaczyniowymi. Ściana wydobywcza o wysokości do 12 m wybierana jest dwuwarstwowo. Pierwsza koparka umieszczona jest na poziomie ok. + 6 m od poziomu przenośnika taśmowego odbiorczego. Współpracuje ona z dwoma przenośnikami mobilnymi (jeden znajduje się na tym samym poziomie co koparka a drugi na poziomie przenośnika odstawczego). Druga z koparek z jednym przenośnikiem mobilnym pracuje na tym samym poziomie co przenośnik taśmowy odstawczy.
Cementownia zlokalizowana jest w Chełmie. Jest producentem cementów portlandzkich, portlandzkich popiołowych wapiennych, mieszanych oraz cementów specjalnych, w tym dla budownictwa drogowego. Posiada certyfikaty Zintegrowanego System Zarządzania zgodne z normami ISO 9001 (jakość), ISO 14001 (środowisko), PN-N 18001 (BHP), ISO 50001 (energia) oraz wymaganiami Rozporządzenia EMAS.
Historia cementowni Chełm
Zakład Cementownia Chełm jest producentem cementu od 1960 roku. Wtedy zostały uruchomione pierwsze piece firmy F.L.Smith pracujące metodą mokrą. Szybki wzrost zapotrzebowania na cement zaowocował w 1970 r. rozbudową zakładu o kolejne piece metody mokrej. Ostatnią dużą i do tej pory najważniejszą inwestycją w zakładzie była budowa nowoczesnej linii produkcji klinkieru metodą suchą.
Klinkier w Chełmie produkowany jest na nowej nitce technologicznej, której rozruch odbył się w II poł. 1999 roku. Jest to linia metody suchej zaprojektowana przez duńską firmę F.L.Smidth. Ten piec był pierwszą pracującą w Polsce instalacją klinkierową zaopatrzoną w kalcynator. Dzięki temu przy swoich niewielkich wymiarach piec osiąga wysoką wydajność (5000 t/dobę). W ślad za dużą wydajnością idą niskie wskaźniki emisji pyłów i gazów oraz niskie koszty produkcji.
Piec jest również unikalny z innego powodu. Jest to typowy piec metody suchej, ale nie posiada silosów mąki surowcowej, a jako młyn surowca, stosuje suszarko-kruszarkę. Takie rozwiązanie spowodowało, że obsługa linii piecowej jest bardziej skomplikowana – dział surowcowy jest tutaj zintegrowany z linią piecową. Z drugiej strony spowodowało to znaczne uproszczenie techniczne i redukcję kosztów operacyjnych.
Technologia produkcji cementu w Cementowni Chełm
Do produkcji klinkieru wykorzystuje się kredę z własnej kopalni oraz glinę, pyły wapienne, dodatki żelazonośne i krzemionkę, pozyskiwane na rynku.
Wykorzystywanie kredy, jako bazowego surowca do produkcji klinkieru (ponad 80%) powoduje, że klinkier produkowany w Chełmie posiada unikalne właściwości i spełnia wysokie wymagania jakościowe wytwarzanych z niego cementów.
Produkcja cementu odbywa się w młynach kulowych w obiegu zamkniętym. Główne składniki cementu - klinkier i gips, są mielone do czasu uzyskania odpowiedniego stopnia rozdrobnienia. Podczas mielenia stosuje się dodatki korygujące i wypełniacze, w zależności od typu produkowanego cementu. Cement jest towarem produkowanym zgodnie z polską normą. Dla zapewnienia klienta o jakości produkowanego cementu, stosuje się kontrolę produkcji na każdym etapie.
W cementowni znajduje się 12 silosów cementu o pojemności 7000 ton każdy. Zakład posiada 2 linie pakowania i paletyzowania cementu wyposażone w pakowaczki firmy Haver&Boecker oraz paletyzatory firmy Beumer. Dodatkowe obie linie wyposażone są w odpowiednie foliomaty.
Cementownia Chełm była jedną z pierwszych cementowni w Polsce, która zainwestowała w rozwój w zakresie spalania paliw alternatywnych, biorąc pod uwagę zarówno koszty produkcji, jak i aspekty ekologiczne. Paliwa alternatywne to odpowiednio wysortowane i przetworzone odpady zawierające energię. Mogą powstawać z odpadów tekstylnych, papierowych, tworzyw sztucznych, zużytych olejów spożywczych i innych – skład i właściwości paliw alternatywnych są szczegółowo regulowane przez przepisy prawne. Spalanie paliw alternatywnych w piecu cementowym jest bezpieczne dzięki jego zaletom. Wysokie temperatury procesu sięgające 2000 stopni Celsjusza długi czas przebywania w palenisku, oraz fakt, że pozostałości popiołu po paliwach wbudowane są w strukturę klinkieru sprawiają, że jest to najbezpieczniejsza metoda znana w przemyśle współspalania odpadów. Mimo to, cementownie nie mogą sobie pozwolić na spalanie dowolnych odpadów. Wynika to z faktu, że konieczne są do uzyskania odpowiednio wysokie temperatury procesu, sięgające 2000ºC aby uzyskać klinkier i cement odpowiedniej jakości. Dlatego też cementownie muszą ściśle kontrolować jakość paliw alternatywnych tak, aby produkty powstające przy ich zastosowaniu, spełniały wymagania wszystkich restrykcyjnych norm. Obecnie Cementownia Chełm jest liderem w Polsce pod względem wykorzystania paliw alternatywnych.
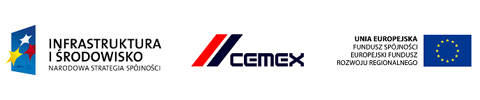
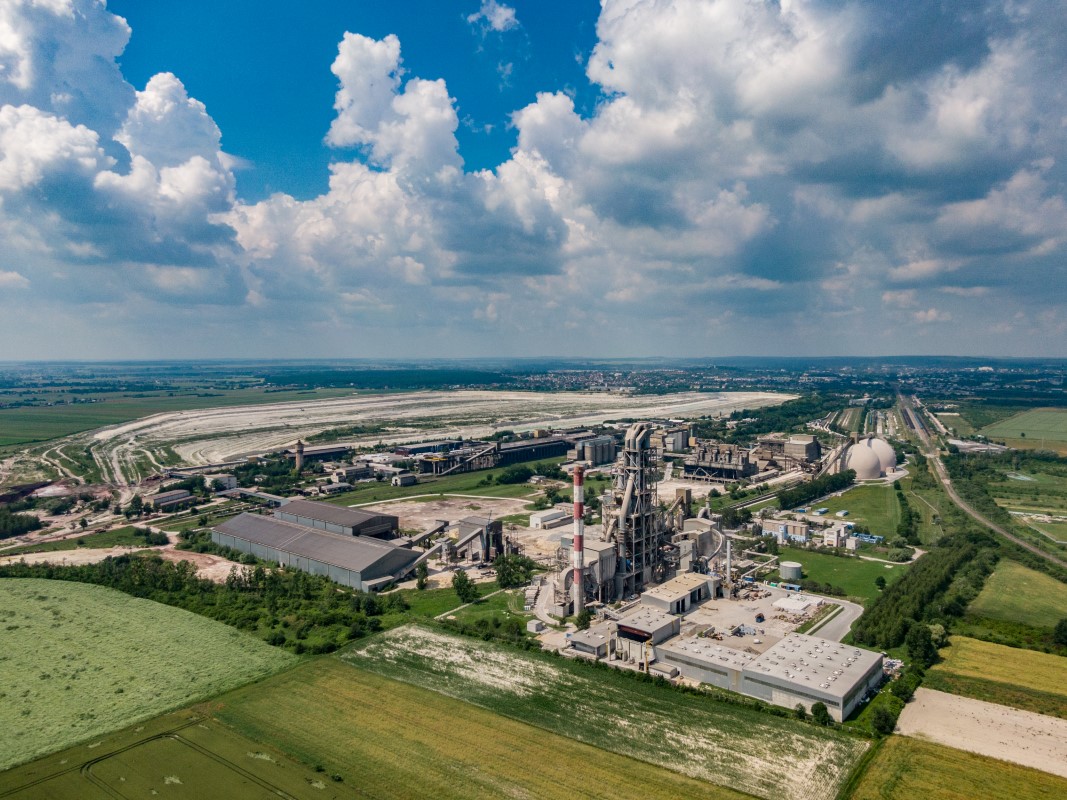
W kwietniu 2011 r. rozpoczęła się największa inwestycja ekologiczna XXI wieku w Cementowni Chełm – budowa dwóch silosów klinkieru o łącznej pojemności 250 tys. ton. Konstrukcja silosów została opracowana przez amerykańską firmę Dometech a ich kształt jest czaszą o średnicy 63,4m i wysokości 43,5m każdy.
Realizacja zadania jest wypełnieniem wymagań pozwolenia zintegrowanego, które nakazuje eliminację emisji niezorganizowanej klinkieru na otwartym składowisku. Ta emisja powoduje okresowo uciążliwość dla okolicznych mieszkańców.
Tak duża pojemność składu pozwoli na przechowywanie całego zapasu klinkieru wewnątrz. Do tej pory ok. 200 tys. ton klinkieru było składowane na zewnątrz, żeby pokryć zwiększone zapotrzebowanie na cement w okresie letnim. Budowa tak dużego składu klinkieru to inwestycja bardzo kosztowna, dlatego firma ubiegała się o dofinansowanie z Funduszy Europejskich. 24 czerwca 2009 roku podpisano umowę o dofinansowanie projektu „Budowa silosów klinkieru w celu realizacji programu dostosowawczego Pozwolenia Zintegrowanego Cementowni Chełm” w ramach działania 4.3 priorytetu IV Programu Operacyjnego Infrastruktura i Środowisko 2007 – 2013. Całkowity kwalifikowany koszt inwestycji wynosi 66 994 000 zł a wielkość refinansowania przez NFOŚ wynosi 20 000 000 zł (prawie 30% całości inwestycji).
Pierwsza kopuła została uruchomiona w listopadzie 2012, a druga w styczniu 2013 r.
Program Operacyjny Infrastruktura i Środowisko 2007–2013
www.pois.gov.pl